Silicone Release Coatings: Solvent-Based VS. Solventless VS. Emulsion
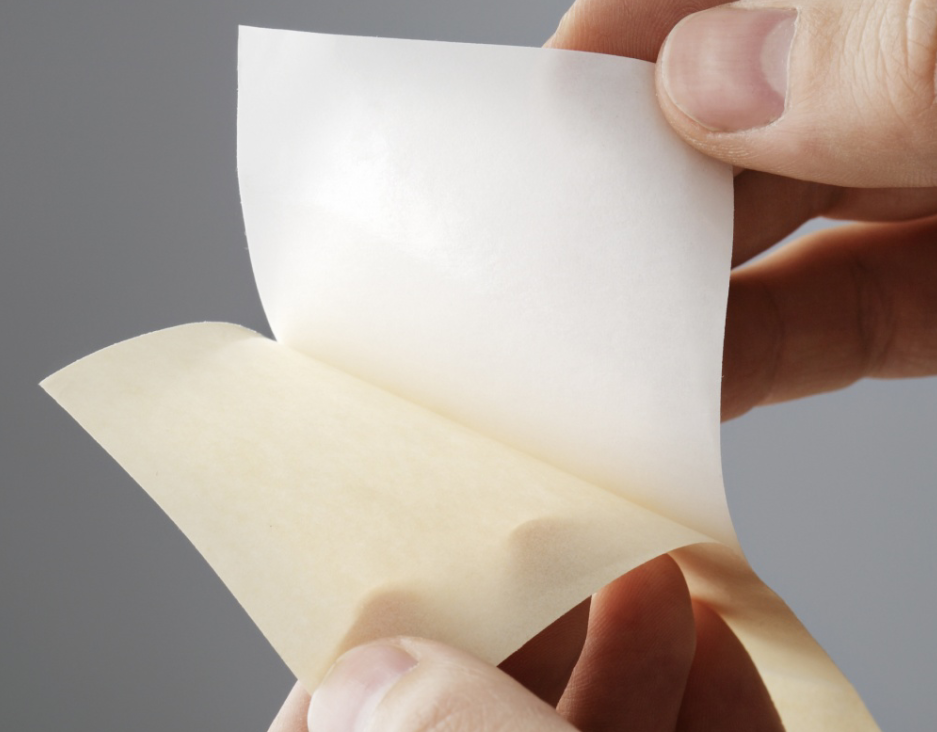
Silicone release coatings are critical in various industries for providing a non-stick surface, typically used in applications like release liners, labels, adhesives, and industrial processes. The three main types of silicone release coatings are solvent-based, solventless, and emulsion coatings. Each type has distinct characteristics, advantages, and limitations. Here’s a comparison of the three:
1. Solvent-Based Silicone Release Coatings
Characteristics:
- Composition: These coatings are silicone polymers dissolved in organic solvents. The solvent acts as a carrier for the silicone, allowing it to be applied evenly to a substrate.
- Curing Process: Typically cured using heat (thermal curing), which evaporates the solvent, leaving behind a cured silicone film.
Advantages:
- High Performance: Provides excellent release properties and is compatible with a wide range of substrates.
- Good Wetting and Coverage: Solvents help achieve smooth, even coatings, especially on challenging surfaces.
- Versatile: Can be tailored for specific release levels and used in applications where high performance is critical, such as in high-speed manufacturing.
Disadvantages:
- Environmental Concerns: The use of volatile organic compounds (VOCs) in solvents raises environmental and health concerns, requiring special handling, ventilation, and disposal processes.
- Regulatory Issues: Increasing regulations on VOC emissions make it challenging to use solvent-based coatings in certain regions or industries.
- Cost: The need for solvents and the associated handling and safety measures can increase production costs.
2. Solventless (100% Solids) Silicone Release Coatings
Characteristics:
- Composition: These coatings consist of 100% reactive silicone polymers with no solvents involved. They are applied as a liquid and cured into a solid film.
- Curing Process: Often cured using thermal methods, ultraviolet (UV) light, or electron beam (EB) curing, depending on the specific formulation.
Advantages:
- Environmentally Friendly: No VOCs are released, making them safer for the environment and easier to comply with regulations.
- Cost-Effective: Lower handling and disposal costs due to the absence of solvents. Also, less energy is required for curing since there’s no need to evaporate solvents.
- High Efficiency: Since there’s no solvent to evaporate, the coating thickness remains consistent, resulting in better control over the release properties.
Disadvantages:
- Application Challenges: Can be more difficult to apply evenly, especially on porous or uneven surfaces. Requires precise application equipment.
- Limited Substrate Compatibility: May not adhere well to certain substrates, particularly those that require solvent interaction to achieve proper bonding.
Characteristics:
- Composition: These coatings consist of silicone polymers dispersed in water (water-based emulsions). The water acts as a carrier, and the silicone is applied as an emulsion.
- Curing Process: Curing involves the evaporation of water, followed by crosslinking of the silicone polymers. Curing can be done thermally or with UV/EB curing, depending on the formulation.
Advantages:
- Low VOCs: Since the primary carrier is water, these coatings emit very low levels of VOCs, making them more environmentally friendly.
- Safe and Easy Handling: Water-based systems are generally safer to handle, store, and dispose of compared to solvent-based systems.
- Good Coverage: Can provide good coverage and uniformity on a variety of substrates, including paper and film.
Disadvantages:
- Longer Drying Time: Water-based systems often require longer drying times, which can slow down production processes.
- Potential for Water Sensitivity: The presence of water can cause issues with moisture-sensitive substrates or lead to incomplete curing in humid environments.
- Limited Performance: In some cases, emulsion-based coatings may not offer the same level of release performance or durability as solvent-based or solventless systems.
Comparison Summary
- Solvent-Based Coatings are high-performing and versatile but come with environmental, regulatory, and cost challenges due to VOC emissions.
- Solventless Coatings are eco-friendly and efficient, with no VOCs, but may be more challenging to apply and may have limited compatibility with certain substrates.
- Emulsion-Based Coatings offer a middle ground with low VOCs and easier handling but may require longer drying times and may not perform as well as the other types in demanding applications.
Choosing the Right Coating
- Solvent-Based Coatings are best for high-performance needs where environmental concerns are secondary, or in applications where the solvent aids in coating performance.
- Solventless Coatings are ideal for situations where environmental impact is a priority, and the substrate is compatible with the coating method.
- Emulsion-Based Coatings are suitable for applications requiring low VOC emissions and safe handling, especially where the substrate can tolerate the longer drying times.
Your choice should consider the specific application, environmental regulations, performance requirements, and cost implications.