Emulsion release coating VS Silicone release coating
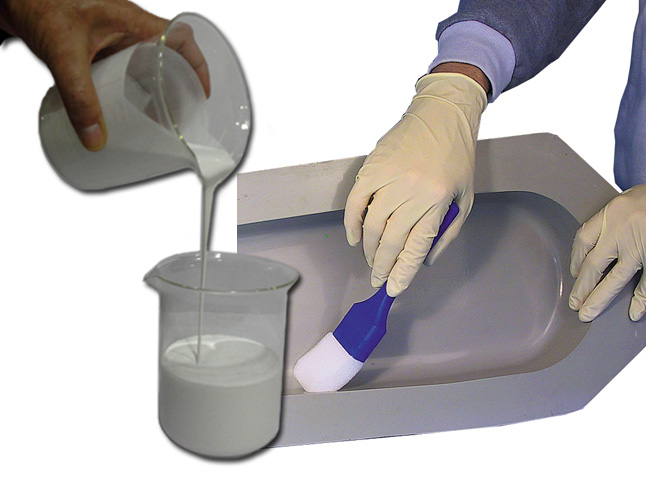
Release coatings are used to create non-stick surfaces on various substrates, enabling easy separation of adhesives, foods, and other materials. Emulsion release coatings and silicone release coatings are two common types of these coatings, each with distinct properties, advantages, and applications.
Composition:
- Emulsion release coatings typically consist of water-based formulations. They may include a mixture of polymers, surfactants, and other additives dispersed in water.
Properties:
- Environmentally Friendly: Being water-based, these coatings are generally more environmentally friendly and have lower VOC (volatile organic compounds) emissions compared to solvent-based coatings.
- Cost-Effective: They are often less expensive due to the lower cost of raw materials and the elimination of solvents.
- Ease of Use: Emulsion coatings are easier to handle and apply, as they can be cleaned up with water.
- Flexibility: They can be formulated to achieve various release levels and other desired properties, such as gloss and printability.
Applications:
- Paper and Film: Used in the production of release liners for labels, tapes, and other adhesive products.
- Textiles: Applied to fabrics to impart non-stick properties.
- Food Industry: Suitable for food packaging applications where non-toxicity and safety are critical.
Composition:
- Silicone release coatings are typically based on silicone polymers, such as polydimethylsiloxane (PDMS). These may be solvent-based, solvent-free, or emulsion-based.
Properties:
- High Release Performance: Silicone coatings provide superior release characteristics, making them highly effective for very sticky materials.
- Temperature Resistance: Silicones can withstand a wide range of temperatures, from very low to very high, without losing their properties.
- Durability: They offer excellent durability and longevity, maintaining their release properties over multiple uses.
- Chemical Resistance: Silicones are resistant to a variety of chemicals, ensuring performance stability in harsh environments.
Applications:
- Labels and Tapes: Widely used as release liners for pressure-sensitive adhesives.
- Medical Applications: Applied to medical release liners and devices due to their biocompatibility.
- Industrial Uses: Suitable for high-temperature and demanding industrial processes, such as composite molding and electronics manufacturing.
Comparison
Environmental Impact:
- Emulsion release coatings are generally more environmentally friendly due to their water-based nature.
- Silicone release coatings, particularly solvent-based ones, may have higher VOC emissions, though advancements in solvent-free and emulsion-based silicones are mitigating this issue.
Cost:
- Emulsion release coatings tend to be more cost-effective.
- Silicone release coatings are often more expensive but provide superior performance, especially for demanding applications.
Performance:
- Silicone release coatings offer better release properties, durability, and temperature resistance.
- Emulsion release coatings are versatile and suitable for less demanding applications where extreme performance is not required.
Application Method:
- Both types can be applied using various methods such as coating, spraying, or dipping. The choice of method depends on the substrate and the specific requirements of the application.
Conclusion
Choosing between emulsion release coatings and silicone release coatings depends on the specific requirements of the application, including environmental considerations, cost, performance needs, and substrate compatibility. Emulsion coatings are ideal for applications where environmental impact and cost are primary concerns, while silicone coatings are preferred for their superior performance and durability in more demanding situations.